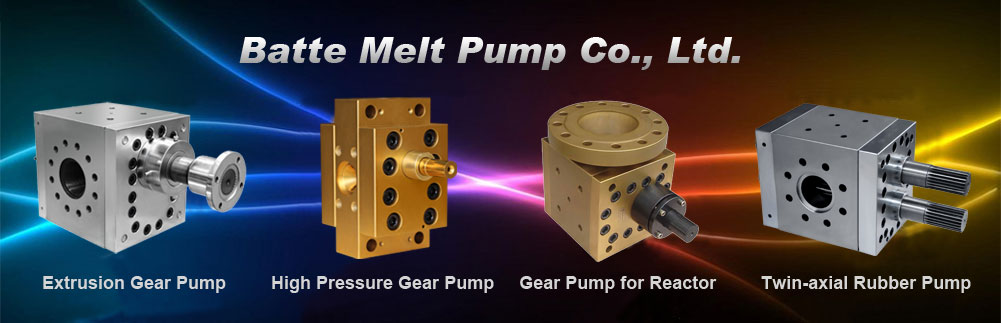
Configuration of melt blown equipment
There are basically two configurations of melt blown equipment. The first is often called "single type" configuration, with a set of independent equipment to produce melt blown or laminated melt blown coil. The second is often referred to as "embedded" configuration, with a set of melt blown equipment as an integral part of other spinning processes (such as spunbond process), such as spunbond melt blown spunbond (SMS).
(1) Single type melt blown device
There are basically three types of nonwovens produced by single type melt blown equipment: filter medium (liquid and air), insulation medium (heat transfer or sound insulation) and absorption medium (absorption). Generally, polypropylene is used as insulation medium and absorption medium, and the area density range is 200-1200g / m2. The requirements for production method and absorption performance are not high. The range of polymers used in filter media is wide, and the surface density is usually 20-300g / m2, which is required to meet the performance index and the width requirements of processed products. Due to the wide and diverse demands of final processing products, spinning elements need to be recycled to reduce waste. The filter medium is usually bonded to another substrate (paper, spunbond nonwovens, glass fibers) to improve its rigidity and withstand the pressure during operation. In addition, the composite product can be folded to increase surface area to improve overall efficiency and service life.
(2) Embedded melt blown device
In the production of sanitary materials and medical SMS and other products, the melt spraying process is used. Melt blown equipment is placed in the existing or new multi-mode head melt spinning production line of polypropylene [S (s) x (XX) s] to improve the product barrier and maintain the required air permeability. The number of the configured die head is completely determined by the target melt blown capacity matching the spunbond production. The ideal matching speed is to maximize the total production efficiency. By weight, SMS composite materials used in the field of health account for about 10% - 15% of the total, and SMS composite materials used in the field of medical use account for about 15% - 25% of the total. The melt blown equipment can also be configured into the existing s (x) s or SS (x) s production line to improve the overall appearance of spunbond products and improve the efficiency of the production line. Due to the decreasing surface density of spunbond products used (depending on market demand), existing and new equipment may not be able to produce the target products with maximum efficiency. For example, in order to produce qualified 17g / m2 spunbond products at a production speed of 600m / min, the equipment is required to have a certain production capacity. To reduce the surface density of the products while maintaining the same production volume means to increase the speed of the production line, which may lead to unqualified products. By adding a set of melt blown components with a surface density of 1-2g / m2, the aim is not only to improve the appearance, but also to offset the low efficiency.

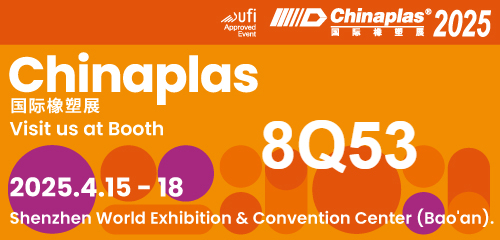
More about screen changer products:
Batte is a professional screen changer manufacturer, supplying screen changer, especially screen changer for extrusion mould