What are the benefits of installing a screen changer downstream of the melt pump?
The screen changer is to filter foreign matter such as carbides and unmelted polymers in the molten polymer, which can prevent the quality of the product from deteriorating. In addition, the screen changer can also filter out large solids that can damage the melt pump. Usually, extrusion screen changer is only installed upstream of the gear melt pump to achieve the above two purposes. However, we recommend installing a screen changer downstream of the Batte melt pump to ensure the quality of the product while saving more than 30% of energy.
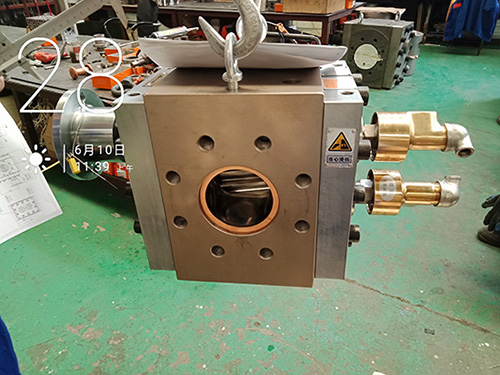
melt pump in extruder
When installed upstream of the melt pump in extruder, hydralulic screen changer is a hindrance to the pressure, so the extruder itself must perform some pressurization; however, compared to the melt pump, the extruder's The boost capacity is relatively low. The extruder will generate additional heat as it pressurizes screen changer for extrusion. In order to achieve the necessary outlet pressure of the extruder, the speed of the extruder must be increased; this will increase the temperature of the polymer, reduce the viscosity of the polymer, and destroy the volumetric efficiency of the equipment; at the same time, it will also lead to a decrease in energy efficiency.
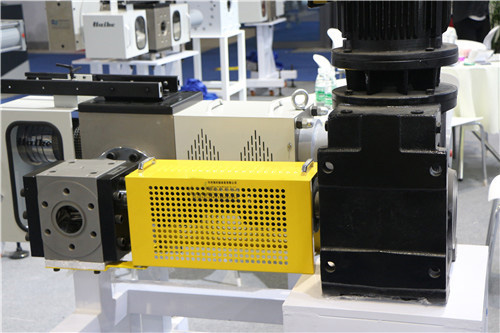
screen changer for plastic extrusion
By adjusting the position of polymer screen changer to the downstream of the melt gear pump, the melt pump for plastic extrusion can fully exert the pressurization function; at the same time, the outlet pressure of the extruder can be reduced. While ensuring the energy saving of the extruder device, the temperature of the polymer can also be lowered and stabilized. However, the volumetric efficiency of the traditional extruder melt pump is low, and only relying on it cannot effectively pressurize the downstream die and screen changer for plastic extrusion. Therefore, it is recommended to install a screen changer downstream of the melt pump.