Is the hydraulic screen changer installed upstream or downstream of the melt pump?
There are usually two options for installing the screen changer in the melt pump: upstream or downstream. The following is a detailed analysis and comparison of two installation positions:
Upstream installation:
When the screen changer is installed upstream of the melt pump, it is an obstacle to pressure. Therefore, the extruder itself must perform certain pressurization. However, compared to the melt pump, the pressure boosting capacity of the extruder is relatively low.
When the extruder pressurizes the screen changer, additional heat is generated. In order to achieve the necessary outlet pressure, the extruder must increase its speed, which will cause an increase in polymer temperature, a decrease in polymer viscosity, and the volumetric efficiency of the equipment will be disrupted, resulting in a decrease in energy efficiency.
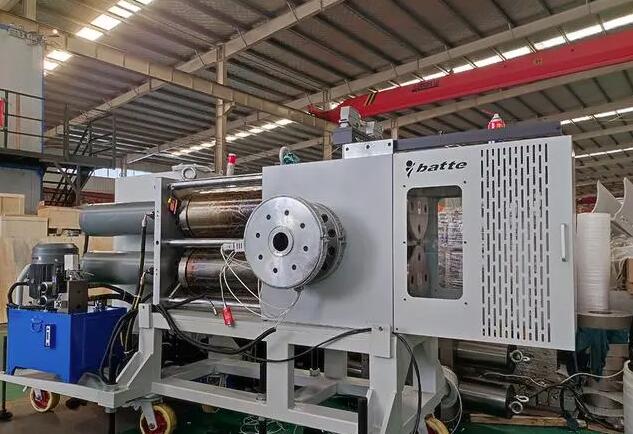
Downstream installation:
Adjusting the position of the screen changer downstream of the melt pump can fully utilize its pressure boosting function while reducing the outlet pressure of the extruder.
This installation method can save more than 30% energy. In addition, it can also lower the temperature of the polymer to stabilize it, thereby ensuring the quality of the product.
When the screen changer is installed downstream, it can filter out foreign objects such as carbides and unmelted polymers in the molten polymer, preventing these impurities from causing damage to the melt pump.
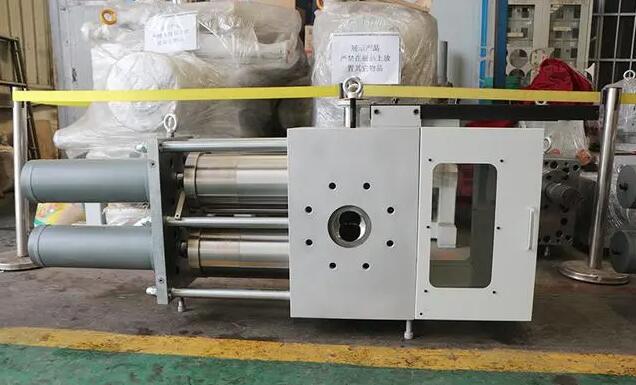
Summary:
Upstream installation: suitable for scenarios that do not require high boosting capacity or require additional heating, but may lead to increased energy consumption and decreased polymer quality.
Downstream installation: suitable for scenarios that require stable pressure, energy conservation, and improved polymer quality. It fully utilizes the pressure boosting function of the melt pump, while reducing energy consumption and polymer temperature.
In practical applications, the installation location of the screen changer should be selected based on specific production needs and equipment performance.
Email: info@battemachinery.com
WhatsApp: +86 158 38331071