What are the differences between the startup valve and the screen changer?
The startup valve and the screen changer both play significant roles in plastic processing and other industrial fields, but they exhibit distinct differences in terms of functionality, structure, and application scenarios.
I. Functional Differences
Startup Valve:
Primarily used for discharging materials and protecting equipment. Before starting the machine, it switches to the discharge position to expel residual materials from the cylinder or pipeline, ensuring that the material is normal before switching to the working position to commence production. In special situations (such as sudden pressure surges), the discharge valve can be set to open, protecting upstream equipment.
In underwater cutting production lines, the startup valve also serves an interlocking function with the underwater cutting control. When unexpected situations arise during underwater cutting, the startup valve triggers an alarm and opens the discharge position, allowing for brief troubleshooting while ensuring the uninterrupted operation of upstream equipment.
Screen Changer:
Primarily used to filter out foreign particles and impurities from the plasticized material flow, ensuring the purity and consistency of product quality.
The screen changer is a manual or automatic switching device that includes one or more screens, allowing for screen changes without stopping the machine, thereby improving production efficiency and product quality.
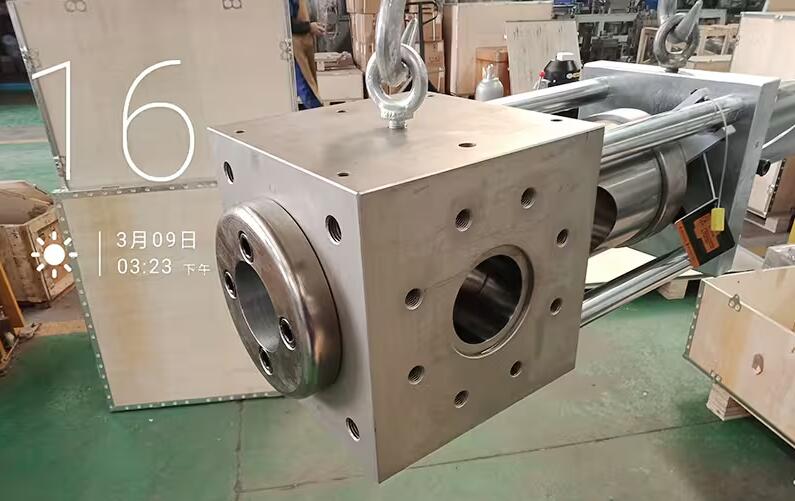
II. Structural Differences
Startup Valve:
Its overall structure resembles a single-plunger, single-column screen changer, featuring a dual-position flow channel; the working position is straight-through, allowing material to flow normally to downstream equipment, while the discharge position is a 90° flow channel for material discharge.
The structure is relatively simple, but the seal is reliable and leak-free, with optimized material flow channel design, eliminating dead zones and stagnation.
Screen Changer:
Comprises one or more screens supported by an alloy porous plate, which is mounted on a plate-type or column-type carrier.
The carrier can be moved to switch between the working position and the offline non-working position within the system.
The structure of the screen changer can be relatively complex, especially for hydraulic automatic screen changers, which include components such as hydraulic stations to achieve rapid screen changes.
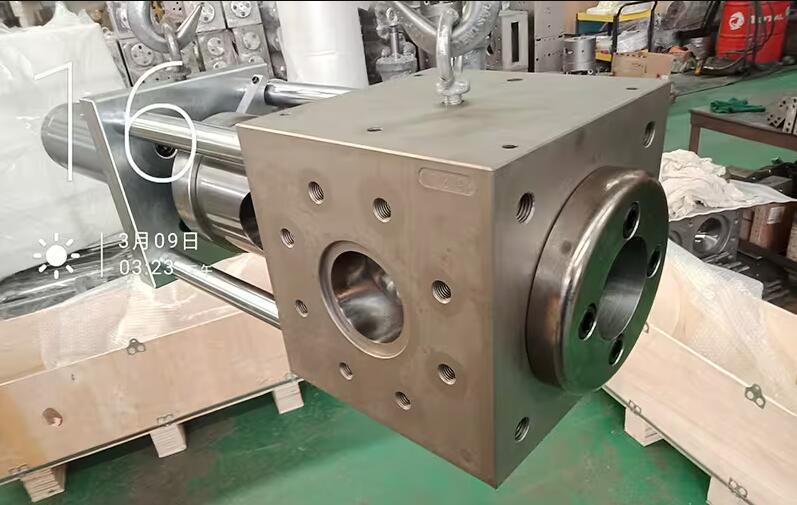
III. Application Scenario Differences
Startup Valve:
Widely used in extrusion production lines, polymerization production lines, and underwater cutting production lines, especially as an essential component in underwater cutting production lines.
Screen Changer:
Can be installed on any new or existing extruders, melt pumps, reactors, or other extrusion production lines.
Widely used in the filtration process of various plastic, rubber, or ceramic melts, ensuring the purity and consistency of product quality.
In summary, the startup valve and the screen changer each have their unique characteristics in terms of functionality, structure, and application scenarios. The startup valve is primarily used for discharging materials and protecting equipment, while the screen changer focuses on filtering impurities and improving product quality. Both play crucial roles in industrial production but require selection and usage based on specific application scenarios and requirements.
Email: info@battemachinery.com
WhatsApp: +86 158 38331071