Application of screen changer for small air-cooled plastic granulation extruder
The application of screen changers for small air-cooled plastic granulating extruders is primarily manifested in the following aspects:
I. Filtering Function
Screen changers play a pivotal role in the plastic granulating extrusion process by effectively filtering out impurities, aged or deteriorated particles, low-grade particulates from recycled materials, various non-plastic substances in recycled materials, and incompatible plastics. If these impurities are not filtered out, they can significantly affect the quality of the final product, potentially causing disruptions in the extrusion process, leading to waste and increased costs.
II. Enhancing Production Efficiency and Product Quality
Uninterrupted Screen Change: The screen changers equipped on small air-cooled plastic granulating extruders often enable screen changes without halting production, ensuring continuity and stability in the production process. This feature is particularly crucial for scenarios requiring continuous production with high efficiency demands.
Improving Product Quality: By filtering out impurities, screen changers significantly enhance the quality of the final product. Additionally, they may increase the backpressure at the die head, improving the plasticization and homogenization of raw materials, resulting in more uniform product texture, better surface finish, and increased pressure resistance values.
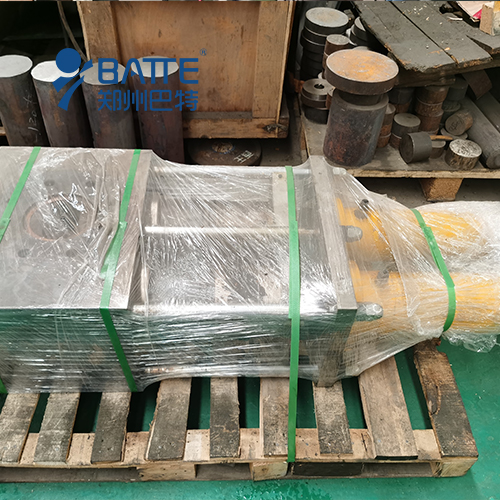
III. Reducing Mold Wear and Energy Consumption
Minimizing Mold Wear: The presence of impurities can accelerate mold wear, but screen changers help reduce this by filtering out impurities, thereby extending the mold's service life.
Energy Saving: The use of screen changers not only enhances production efficiency but also contributes to energy savings. By ensuring production continuity and stability, it minimizes energy losses associated with stopping the extrusion process for screen changes.
IV. Technical Characteristics and Configurations
Types of Screen Changers: Small air-cooled plastic granulating extruders offer a variety of screen changer types, including continuous belt-type, rotary, plate-type, and columnar. Among them, plate-type and columnar screen changers are widely adopted due to their mature technology, simple manufacturing, low operational costs, and ease of installation.
Materials and Structure: The material selection for screen changer components is crucial, with alloy steel typically used, especially for sealing components and switching devices, which undergo special heat treatment to achieve high hardness and wear resistance. The filter screen usually consists of several layers of meshes with different mesh sizes, where the outer coarse mesh prevents larger particles from entering the inner fine mesh, which filters out small solid particles from the melt.
Power Systems: Screen changer power systems are generally divided into hydraulic drive and direct motor drive. Hydraulic drive operates through hydraulic oil actuating cylinders to move the slide plate or screen column for screen changes; direct motor drive utilizes a motor to move the slide plate up and down via a lead screw for screen changes.
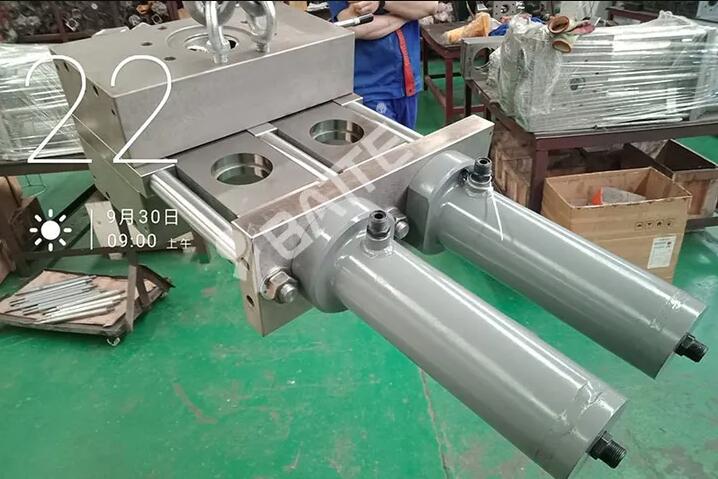
V. Application Scenarios
Screen changers for small air-cooled plastic granulating extruders are primarily used in plastic granulating production lines that require high continuity and uninterrupted screen changes. These production lines may include the production of PE, PP, PPR, PERT pipes, sheets, films, cast films, non-woven fabrics, and chemical fiber spinning, among others. In these applications, screen changers play a vital role in ensuring production continuity and stability, improving product quality, and enhancing production efficiency.
In conclusion, screen changers for small air-cooled plastic granulating extruders hold extensive application prospects and significant value in the plastic processing industry.
Email: info@battemachinery.com
WhatsApp: +86 158 38331071