What methods can be used to reduce errors in calculating the filtration area of a screen changer?
Precise Analysis of Plastic Melt Characteristics
Detailed Composition Testing: Before calculating the filtration area, it is essential to conduct a detailed composition analysis of the recycled plastic. Equipment such as Fourier Transform Infrared Spectroscopy (FT-IR) and Differential Scanning Calorimetry (DSC) can be used to determine the proportions of various components in the recycled plastic. For example, FT-IR analysis can accurately identify the types and contents of different polymers in the plastic, such as distinguishing between polyethylene, polypropylene, and their copolymers. With this accurate composition information, the characteristics of the plastic melt, such as viscosity, can be better estimated, thereby enabling more precise calculation of the filtration area.
Rheological Testing: Rheological testing of recycled plastic provides accurate data on the melt viscosity as it changes with factors such as temperature and shear rate. A rotational rheometer can measure the viscosity of plastic melts at different temperatures and shear rates. For example, for a high-viscosity recycled PVC plastic, rheological testing can obtain its viscosity curve at different temperatures. When calculating the filtration area, the viscosity at the actual extrusion temperature can be used to determine a more accurate filtration velocity, thereby reducing calculation errors.
Impurity Analysis and Quantification: Besides the plastic composition, impurities also need to be analyzed and quantified. Methods such as mechanical sieving and optical microscope observation can be used to determine the type, size distribution, and content of impurities. For example, mechanical sieving can classify the impurities in recycled plastic by size, and then the weight proportion of impurities in different size ranges can be calculated. With detailed information on impurities, the filtration area calculation can be more accurately adjusted based on their impact on screen clogging.
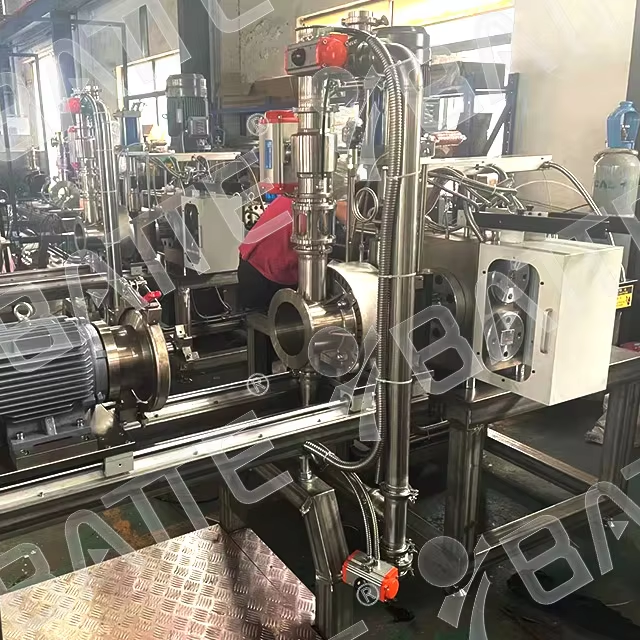
Optimized Equipment Selection and Matching
Reasonable Selection of Screen Changer Type: Based on the characteristics of the recycled plastic and the parameters of the extruder, an appropriate type of screen changer should be selected. For example, for recycled plastics with high viscosity and high impurity content, double-column double-station screen changers or mesh belt automatic screen changers may be more suitable. These screen changers have larger filtration areas and better anti-clogging performance. At the same time, the internal structure of the screen changer, such as the support method of the filter screen and the design of the melt channel, should be considered. Screen changers that can enable uniform melt distribution and reduce dead zones should be selected to improve filtration efficiency and calculation accuracy.
Precise Matching of Extruder and Screen Changer: Ensuring good matching between the extruder and the screen changer is crucial. The screen changer should be selected based on parameters such as the extruder screw diameter, length-to-diameter ratio, and speed range. Generally, the larger the extruder screw diameter and the higher the length-to-diameter ratio, the greater the melt flow rate, and a screen changer with a larger filtration area should be selected. For example, for a twin-screw extruder with a diameter of 100mm and a length-to-diameter ratio of 30:1, which has a large melt flow rate, a screen changer with a sufficiently large filtration area should be equipped to ensure accurate filtration results.
Calibration of Pressure and Flow Measurement Equipment: To obtain accurate melt pressure and flow data, the measurement equipment needs to be regularly calibrated. Pressure sensors can be calibrated using standard pressure sources, and flow meters can be calibrated using standard flow calibration devices. For example, high-precision piston-type pressure gauges can be used to calibrate pressure sensors to ensure that the pressure measurement error is within the allowable range. Accurate pressure and flow data are the foundation for precise calculation of the filtration area.
Strict Process and Operational Control
Precise Temperature Control: During the extrusion process, the temperature should be precisely controlled to reduce the impact of temperature fluctuations on the viscosity of the plastic melt. High-precision temperature controllers and heating/cooling systems should be used to ensure temperature accuracy. For example, for some temperature-sensitive recycled plastics, such as PET, the temperature control accuracy can reach ±1℃. Temperature monitoring points can also be set near the screen changer to promptly detect and adjust any possible local temperature changes, keeping the viscosity of the plastic melt relatively stable and improving the accuracy of filtration area calculation.
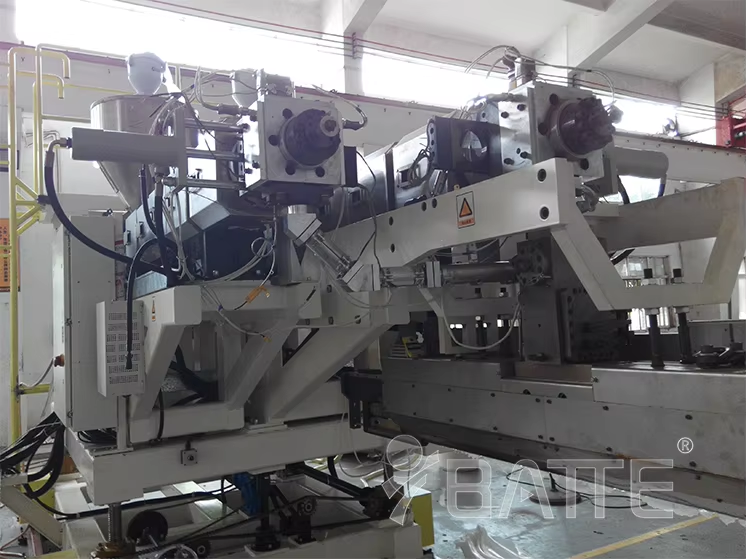
Stable Screw Speed: By optimizing the motor control system of the extruder, the stability of the screw speed can be ensured. A closed-loop control system can be adopted to monitor and adjust the output power of the motor in real-time based on the set speed value, reducing speed fluctuations. For example, in some advanced extruder control systems, the fluctuation of the screw speed can be controlled within ±1%. A stable screw speed can ensure stable plastic melt flow, which is beneficial for accurate calculation of the filtration area.
Standardized Screen Replacement and Cleaning Procedures: Establish strict screen replacement and cleaning procedures, and determine a reasonable replacement cycle based on the impurity content of the recycled plastic and production conditions. When cleaning the screen, appropriate cleaning methods should be used to avoid damaging the screen or altering its performance. For example, for fine screens, ultrasonic cleaning equipment can be used, which can effectively remove impurities while maintaining the original performance of the screen. Standardized operating procedures can ensure that the effective filtration area of the screen remains relatively stable, reducing calculation errors.
Email: info@battemachinery.com
WhatsApp: +86 158 38331071