Plastic Extrusion Manual Screen Changer: Enhancing Efficiency and Quality in Polymer Processing
The plastic extrusion process is a cornerstone of modern manufacturing, enabling the production of a wide range of products, from pipes and profiles to films and sheets. At the heart of this process lies the screen changer, a critical component that ensures the quality and consistency of the final product. Among the various types of screen changers available, the manual screen changer remains a popular choice for many extrusion operations due to its simplicity, reliability, and cost-effectiveness. This article explores the role, functionality, and benefits of manual screen changers in plastic extrusion.
What is a Manual Screen Changer?
A manual screen changer is a device used in plastic extrusion systems to filter out contaminants, such as dirt, gels, or unmelted polymer particles, from the molten plastic before it passes through the die. It consists of a series of metal screens with varying mesh sizes, housed in a plate or cartridge. These screens act as filters, trapping impurities and ensuring a clean, homogeneous melt flow.
Unlike automatic or hydraulic screen changers, manual screen changers require operator intervention to replace the screens when they become clogged or need to be changed for a different filtration level. While this may seem like a drawback, manual screen changers offer several advantages, particularly for smaller-scale operations or applications where frequent screen changes are not required.
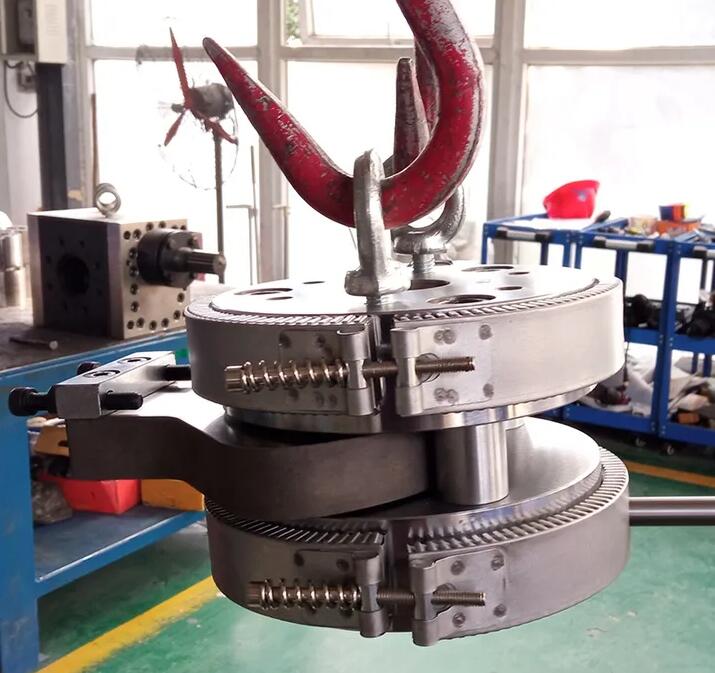
How Does a Manual Screen Changer Work?
The operation of a manual screen changer is straightforward:
Filtration: As the molten plastic flows through the extruder, it passes through the screen pack, which captures impurities and prevents them from reaching the die.
Pressure Build-Up: Over time, the screens become clogged with contaminants, leading to an increase in pressure upstream of the screen changer.
Screen Replacement: When the pressure reaches a predetermined threshold, the extrusion process is paused. The operator manually removes the old screen pack and replaces it with a new one.
Resumption of Extrusion: Once the new screens are in place, the extrusion process resumes, ensuring consistent product quality.
Advantages of Manual Screen Changers
Cost-Effectiveness: Manual screen changers are generally more affordable than their automatic or hydraulic counterparts. They have fewer moving parts, which reduces both initial costs and maintenance expenses.
Simplicity: The design of manual screen changers is simple and robust, making them easy to operate and maintain. This simplicity also minimizes the risk of mechanical failure.
Flexibility: Manual screen changers allow operators to easily switch between different screen mesh sizes or types, depending on the specific requirements of the extrusion process.
Suitability for Small-Scale Operations: For smaller production runs or operations with limited budgets, manual screen changers provide an effective solution without the need for complex automation.
Reliability: With fewer components and no reliance on hydraulic or pneumatic systems, manual screen changers are highly reliable and can operate in harsh environments.
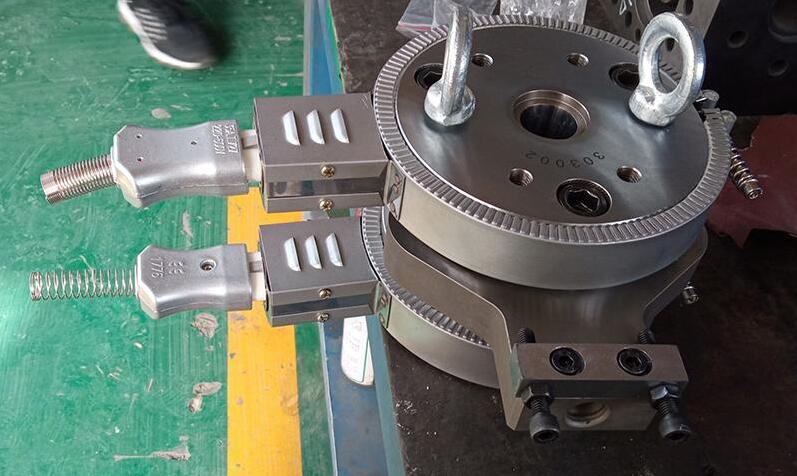
Applications of Manual Screen Changers
Manual screen changers are widely used in various plastic extrusion applications, including:
Pipe and Profile Extrusion: Ensuring clean, defect-free surfaces in products like PVC pipes and window profiles.
Film and Sheet Extrusion: Maintaining consistent thickness and clarity in plastic films and sheets.
Blow Molding: Filtering contaminants to improve the quality of hollow plastic products, such as bottles and containers.
Cable and Wire Coating: Preventing impurities from affecting the insulation or jacketing of cables and wires.
Limitations of Manual Screen Changers
While manual screen changers offer numerous benefits, they do have some limitations:
Downtime: The need to pause the extrusion process for screen replacement can lead to production downtime, which may not be ideal for high-volume operations.
Labor-Intensive: Manual screen changers require operator intervention, which can increase labor costs and the risk of human error.
Pressure Fluctuations: The process of changing screens can cause pressure fluctuations in the extruder, potentially affecting product consistency.
Choosing the Right Screen Changer for Your Operation
When deciding whether a manual screen changer is the right choice for your extrusion process, consider the following factors:
Production Volume: Manual screen changers are best suited for low- to medium-volume production. For high-volume operations, automatic or hydraulic screen changers may be more efficient.
Material Type: Some materials, such as recycled plastics, may contain more contaminants and require frequent screen changes, making manual systems less practical.
Budget: If cost is a primary concern, a manual screen changer offers a cost-effective solution without compromising on quality.
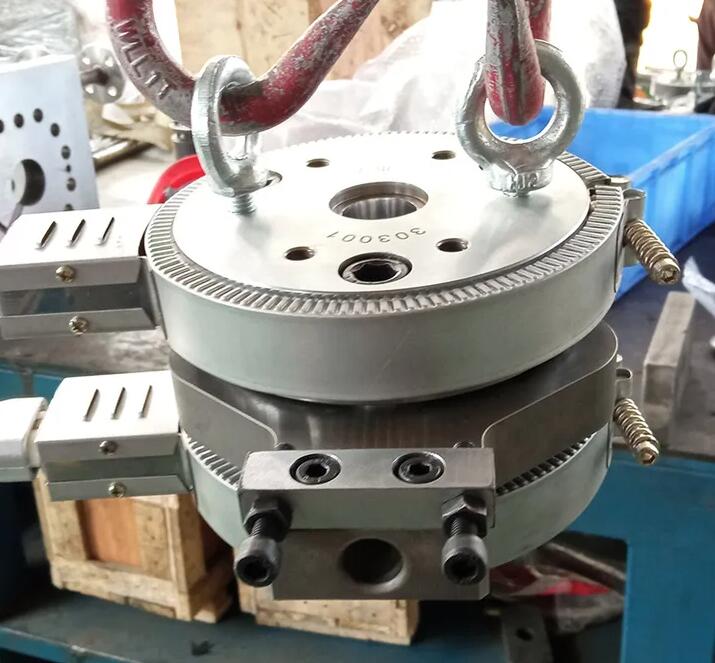
The manual screen changer remains a vital tool in the plastic extrusion industry, offering a simple, reliable, and cost-effective solution for filtering contaminants and ensuring product quality. While it may not be suitable for every application, its advantages make it an excellent choice for smaller-scale operations or processes where frequent screen changes are not required. By understanding the role and functionality of manual screen changers, manufacturers can make informed decisions to optimize their extrusion processes and deliver high-quality products to their customers.
Email: info@battemachinery.com
WhatsApp: +86 158 38331071