Screen Changer for Plastic Break Machinery: Detailed Information and Explanation
I. Definition and Function
The screen changer is a crucial component in plastic breaking machinery, primarily used for filtering molten plastic to remove impurities and particles, ensuring the purity and quality of plastic products. During the plastic processing process, when molten plastic passes through the screen changer, impurities and particles are retained by the filter screen, while pure plastic continues to flow to the next process.
II. Types and Structure
Screen changers come in various types, including manual, semi-automatic, and fully automatic screen changers. Their structure typically includes components such as the filter screen, mold plate, and sealing assembly. The filter screen is the core component of the screen changer, used to retain impurities and particles; the mold plate supports and fixes the filter screen; and the sealing assembly ensures that molten plastic does not leak when passing through the screen changer.
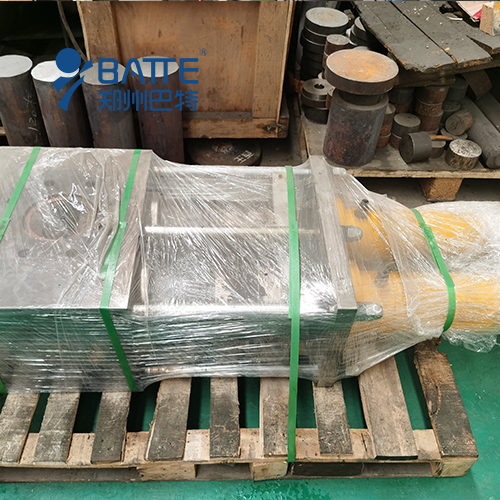
III. Operating Principle
When molten plastic passes through the screen changer, the filter screen retains impurities and particles within it. As production time increases, the filter screen gradually becomes clogged, impeding the flow of plastic. At this point, it is necessary to stop the machine and replace the filter screen. Manual screen changers require manual disassembly and installation of the filter screen, while semi-automatic and fully automatic screen changers can achieve rapid replacement of the filter screen through mechanical equipment, reducing downtime and improving production efficiency.
IV. Application and Advantages
Screen changers are widely used in various plastic processing machinery, such as plastic extruders and plastic injection molding machines. In plastic breaking machinery, screen changers also play an important role in ensuring that crushed plastic particles are pure and free of impurities.
The advantages of using a screen changer mainly include:
Improving Product Quality: By filtering impurities and particles from molten plastic, the screen changer can significantly improve the purity and quality of plastic products.
Reducing Downtime: Semi-automatic and fully automatic screen changers can achieve rapid replacement of the filter screen, reducing downtime and improving production efficiency.
Lowering Maintenance Costs: The screen changer is designed reasonably with a simple structure, making it easy to maintain and service, thereby reducing maintenance costs.
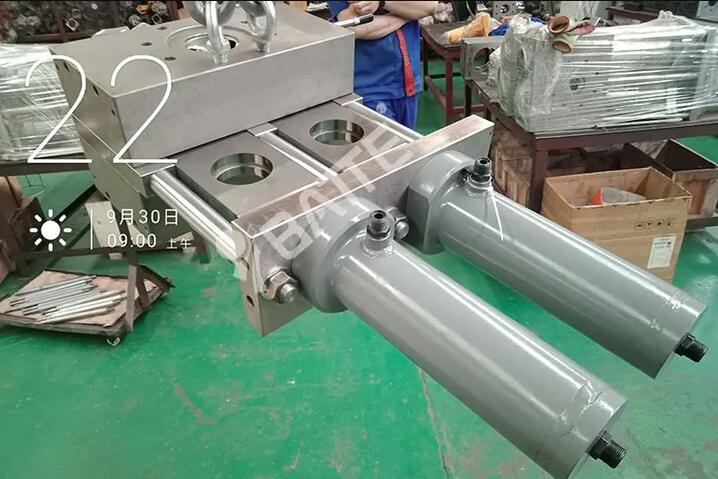
V. Purchasing and Maintenance Suggestions
When purchasing a screen changer, consider the following factors:
Filter Screen Material: Choose a filter screen material that is resistant to high temperatures and corrosion to ensure the service life and filtering effect of the screen changer.
Screen Changing Method: Select an appropriate screen changing method based on production needs, such as manual, semi-automatic, or fully automatic.
Brand and Reputation: Choose a well-known brand and a supplier with a good reputation to ensure the quality and after-sales service of the screen changer.
When maintaining a screen changer, pay attention to the following matters:
Regularly Clean the Filter Screen: Regularly cleaning the filter screen can remove impurities and particles attached to it, maintaining its filtering effect.
Inspect Sealing Components: Regularly inspect the wear of sealing components and replace severely worn sealing components in a timely manner to prevent molten plastic leakage.
Lubrication and Maintenance: Regularly lubricate and maintain the sliding components of the screen changer to ensure its normal operation and extend its service life.
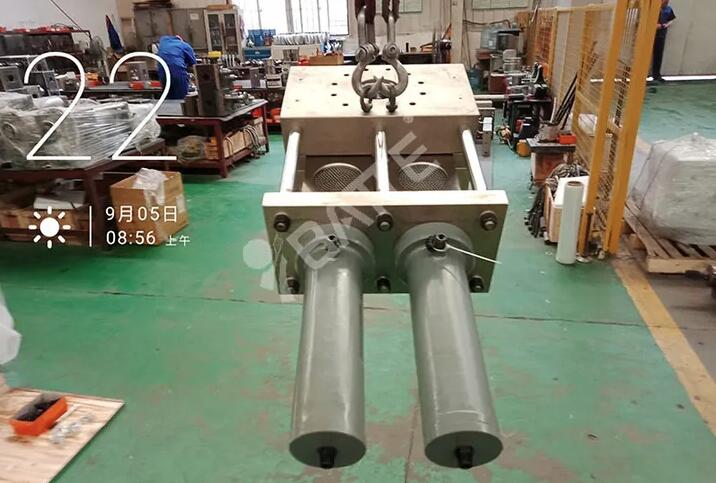
In summary, hydraulic screen changers play an important role in plastic breaking machinery, helping to improve product quality, reduce downtime, and lower maintenance costs. When purchasing and maintaining screen changers, consider factors such as filter screen material, screen changing method, brand, and reputation, and pay attention to regular cleaning of the filter screen, inspection of sealing components, and lubrication and maintenance.
Email: info@battemachinery.com
WhatsApp: +86 158 38331071