continuous screen exchanger for XPS plant
Regarding the continuous screen changer in XPS (extruded polystyrene) factories, the following is a detailed introduction:
I. Overview of XPS Factories
XPS is an excellent thermal insulation material widely used in construction, packaging, refrigeration, and freezing industries. With the increasing demand for high-performance materials, the production processes and equipment for XPS have been continuously improved to enhance production efficiency, reduce costs, and improve product quality.
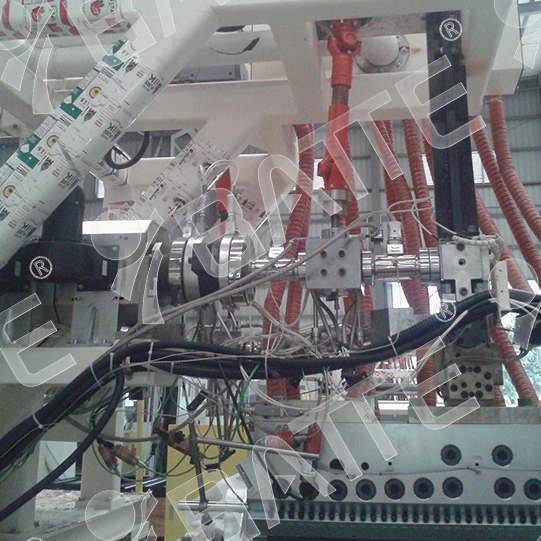
II. The Importance of Continuous Screen Exchangers in XPS Production
In the production process of XPS, plastic melt needs to be heated, plasticized, and extruded through an extruder. However, the melt may contain impurities or degradation products, which can affect the quality of the final product if not removed promptly. Therefore, a screen exchanger is installed in the extruder to filter out impurities in the melt. Traditional manual screen exchangers require downtime for filter screen replacement, which not only affects production efficiency but may also cause melt degradation and unstable product quality. In contrast, continuous screen exchangers can replace the filter screens without stopping the production process, ensuring continuity and stability of production.
III. Working Principle of Continuous Screen Exchangers
A continuous screen exchanger typically consists of a housing, inner rollers, filter screen installation slots, material flow paths, and sealing structures. Its working principle is as follows: Material Entry: The material enters the internal space of the screen exchanger through the material inlet. Filtration: As the material passes through the filter screen, impurities are blocked on one side of the screen. Material Outlet: The filtered material flows out of the screen exchanger along the material flow path. Filter Screen Replacement: When the filter screen becomes clogged to a certain extent, the installation slot rotates to a position opposite the screen exchange port, and a new filter screen is inserted into the slot while the clogged screen is removed.

IV. Advantages of Continuous Screen Exchangers
Improved Production Efficiency: There is no need to stop the production for filter screen replacement, reducing production downtime. Enhanced Product Quality: Continuous filtration ensures the cleanliness of the melt, reducing the impact of impurities on the product. Reduced Labor Intensity: The operation of manually replacing filter screens is reduced, lowering the labor intensity for workers. Extended Equipment Lifespan: The thermal shock and mechanical wear on the extruder caused by downtime for filter screen replacement are reduced.
V. Application in XPS Factories
In XPS factories, continuous screen exchangers are typically installed on the melt pipeline of the extruder. By selecting appropriate types and specifications of filter screens, impurities in the melt can be effectively removed, ensuring the quality of the final product. At the same time, continuous screen exchangers can be used in conjunction with other equipment (such as melt pumps, die heads, etc.) to achieve more efficient and stable production.
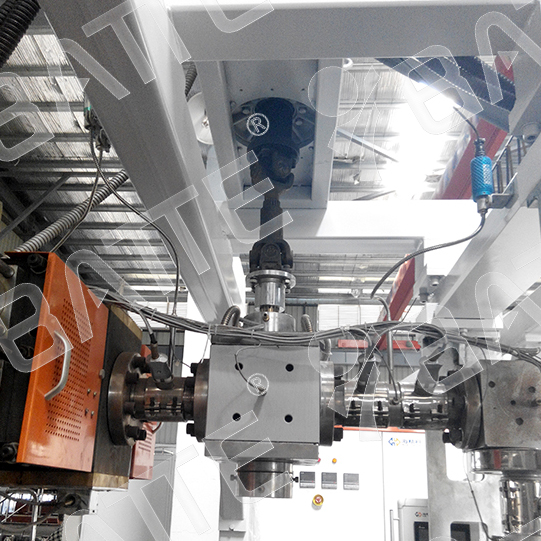
Continuous screen changers play a crucial role in XPS factories. They can replace filter screens without stopping the production process, improving production efficiency, product quality, and equipment lifespan. With continuous technological advancements, the performance and reliability of continuous screen exchangers will continue to improve, providing stronger support for the production of XPS and other plastic products.
Email: info@battemachinery.com
WhatsApp: +86 158 38331071