Masterbatch pelletizing double-plate non-stop screen changer
Masterbatch pelletizing double-plate screen changer: alternate screen changing without stopping, stable pressure and zero leakage! Double runner and double station design guarantees continuous production, automatic alarm monitors the screen status in real time, and hydraulic drive takes only a few seconds to change the screen. Suitable for all kinds of extruders, covering the whole scene of chemical fiber, film, pipe, etc. The energy storage sealing structure prevents leakage at high temperature and high pressure, so that efficient production and stable quality can be achieved at the same time.
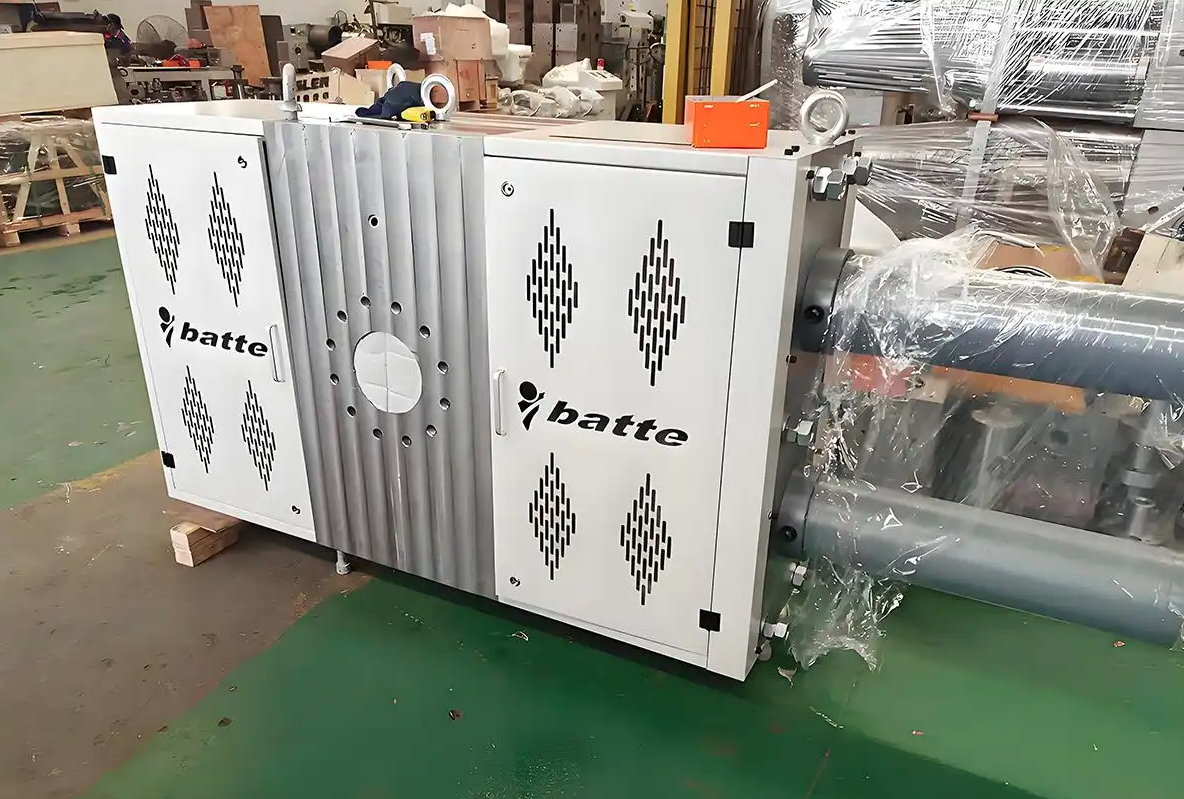
Structure of masterbatch pelletizing double-plate screen changer
The masterbatch granulating double-plate non-stop screen changer is mainly composed of the following parts:
Two parallel skateboards: each skateboard has a filtering station, which ensures that the double stations work at the same time and improves the production efficiency.
The main body of the screen changer: used to support and accommodate the two slide plates and the filter screen to ensure a stable flow of the plastic melt during the screen changing process.
Hydraulic system: responsible for driving the movement of the slide plate to realize the screen changer operation. Power is provided through a hydraulic station to drive the slide plates in and out of the screen changer body.
Control System: Usually includes pressure sensors, alarm system, etc., which is used to monitor the screen status and trigger an alarm when needed.
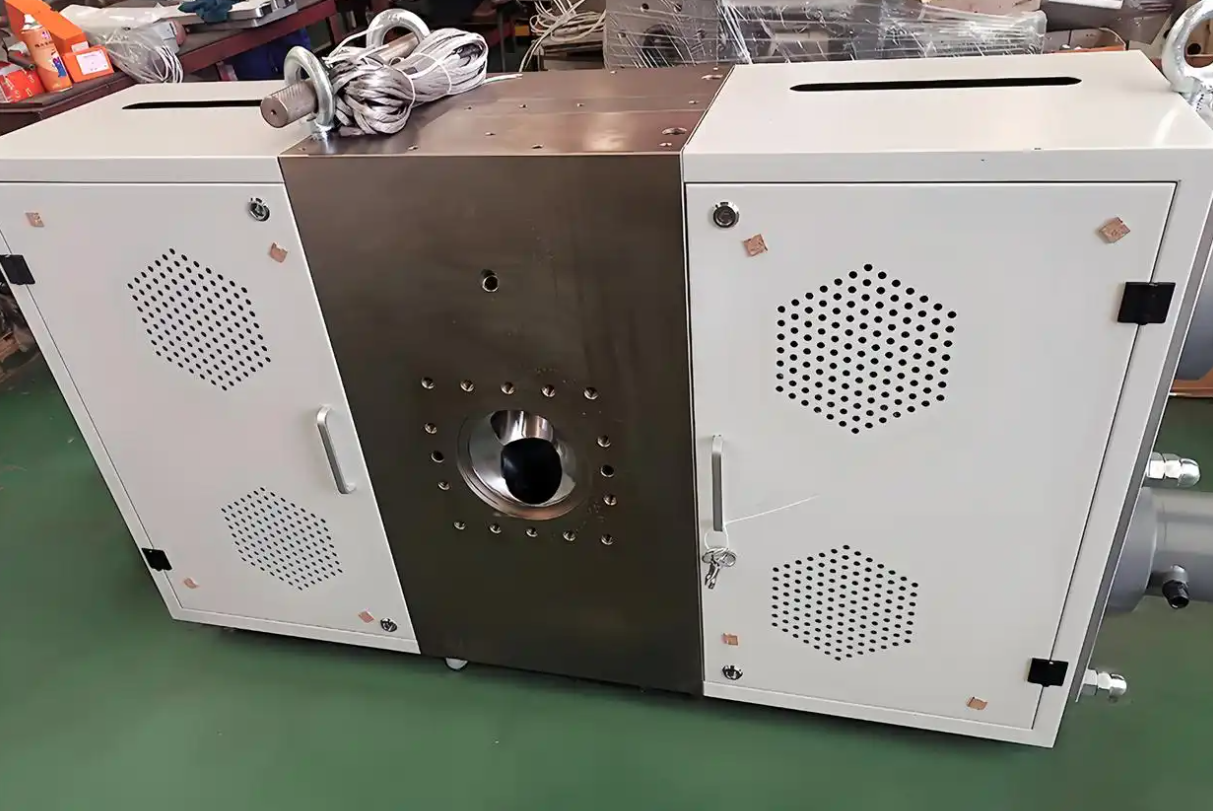
Second, masterbatch granulation double plate screen changer features
Double runner double station: the design of two parallel sliding plate makes the screen changer have double runner double station, which can work at the same time and improve the production efficiency.
Alternate screen changing: when the screen on one slide plate needs to be replaced, the other slide plate continues to work to ensure the continuity of production. This design avoids interruption of production due to screen change.
Small pressure fluctuation: As the double stations work at the same time, when changing the screen, one screen works and the other screen is replaced, so the process of changing the screen will not cause obvious fluctuation to the production of the extruder, which ensures the stability of the quality of the products.
Simple structure, easy to operate: the structure design of the double-plate screen changer is relatively simple, easy to operate and maintain. The screen changing process can be completed by simple operations such as the handle button on the hydraulic station.
Automatic alarm: When the filter screen is clogged or impurities accumulate to a certain level, the pressure sensor will trigger the alarm system to remind the operator to change the screen in time to ensure the smooth running of the production process.
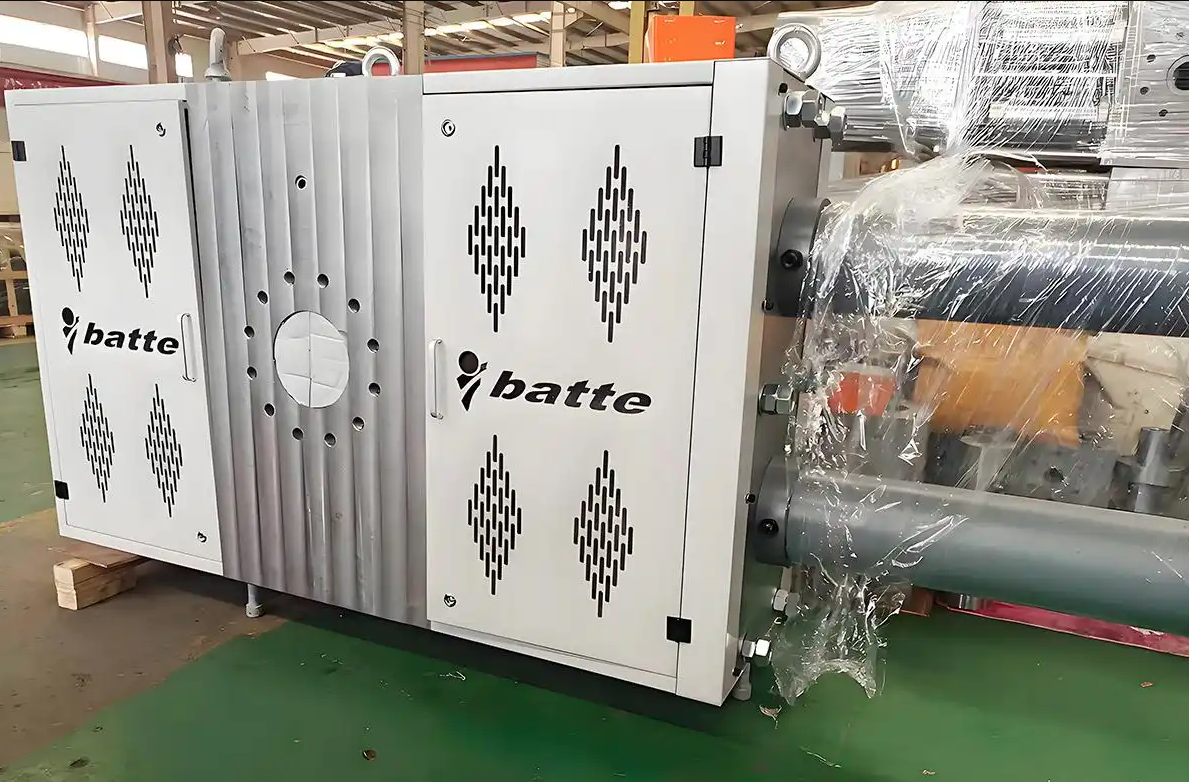
Wide range of application: the double-plate non-stop screen changer is suitable for almost all polymer melt filtration and can be used with different standard single-screw or twin-screw extruders. Widely used in chemical fiber, blown film, flat film, cast film production, pipe, plate, wire, fiber manufacturing, pelletizing line, recycling and many other fields.
Good sealing performance: It adopts reliable sealing structure, such as flexible pressure-activated sealing structure or circulating water channel cooling sealing, etc., which ensures that the material will not leak under high-pressure and high-temperature environment, and avoids the pollution of the production environment and the waste of material.
Fast screen changing speed: matched with accumulator hydraulic station, the screen changing time is short, and it can complete the screen changing operation quickly to ensure the high efficiency of production.
Email: sale@meltpump.com
WhatsApp: +86 158 38331071